Hello everyone,
some projects take much longer than you might think.
This is not only the case with public building projects, but also with the restoration of some fixtures.
In the early seventies, the HOLOPHANE company launched a post-top fixture whose housing consisted of two thick-walled ball halves made of pressed glass.
There were different sizes of this fixture. The smaller version presented here has a diameter of 400mm.
This version was originally designed for incandescent lamps from 150W to 300W, high-pressure mercury vapor lamps 125W or mixed light lamps 250W.
A look at three catalog pages from EUROPHANE (the company HOLOPHANE changed its name) at the beginning of the eighties:

Source: EUROPHANE catalog 1980

Source: EUROPHANE catalog 1980

Source: EUROPHANE catalog 1980
These ball halves are glued together, so that no moisture or dirt can penetrate the inside of the luminaire through these points.
In the course of the production of this fixture, there were always small technical changes. Most of the changes were aimed at reducing manufacturing costs and in the first years of production,
the upper and lower parts of the fixture were made of die-cast aluminum. Likewise the two rings, that hold the glass ball halves together with threaded rods.
In the later years of production, the upper and lower parts of the fixture were made of GRP and the two rings for mechanically holding the two glass ball halves together were pressed from sheet metal.
In 2019, I bought this fixture used in France for €100. That was already a “bargain” at the time, because these “Boule HOLOPHANE” are often bought by "high-end butchers" and then resold in a chic way for several 100€ as a fancy light for a LOFT.
So the problem starts with finding an affordable unrestored fixture in the first place. It worked.
The inside of the fixture had the usual impurities, just like other lamps.
What was particularly noticeable, however, was that it must have gotten very warm inside the fixture. The connecting cables to the E27 lamp holder were more than brittle.
There may have been a 250W mixed light bulb in this fixture, which had “heated up” well. A ballast was
not present when this fixture was taken over, only the holes for it in the gear tray had been drilled at the factory.

The extent to which the cable sheathing has already disintegrated is clearly visible. After cleaning, new cables were installed.
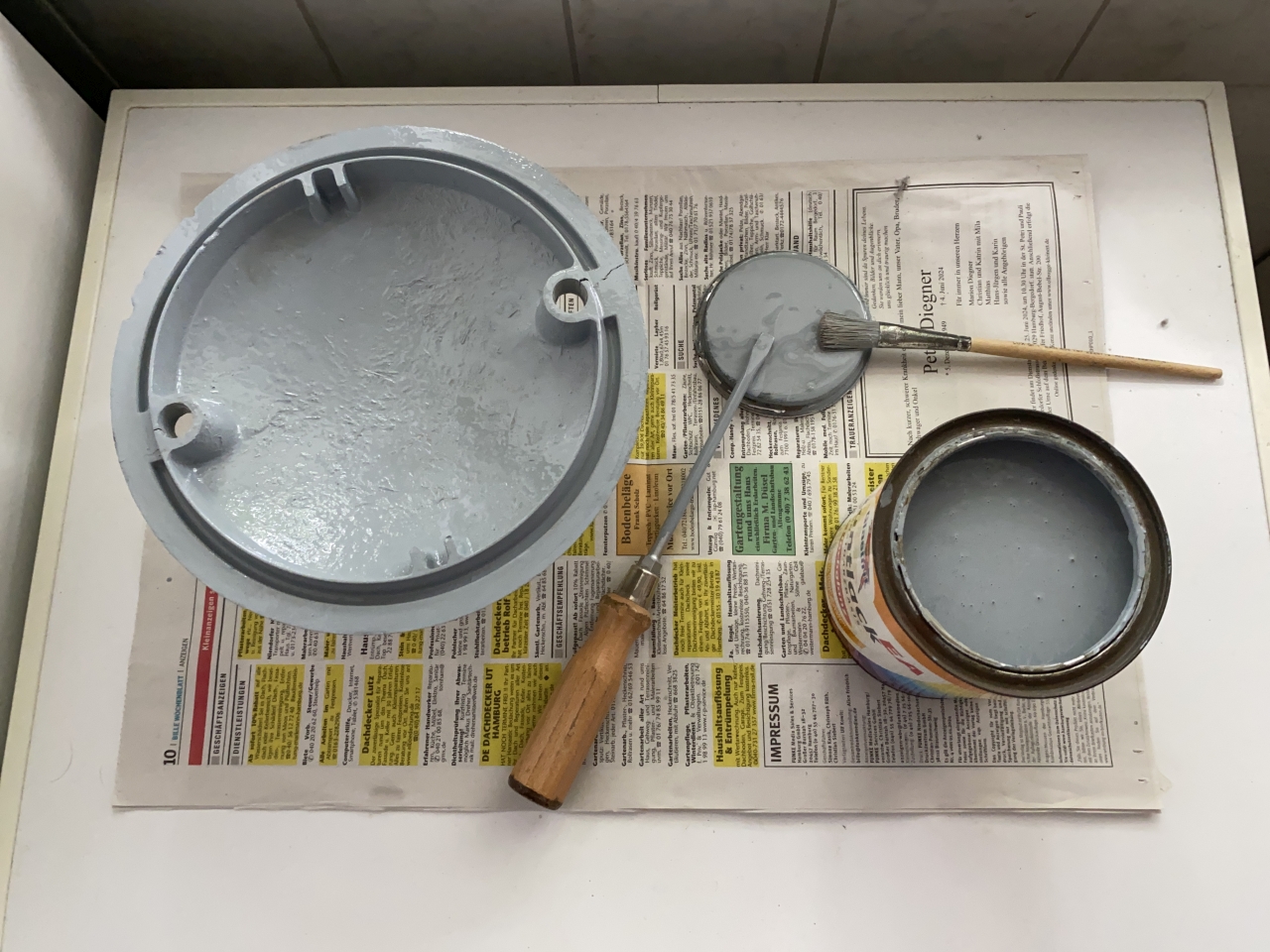
The upper and lower parts of the fixture are made of GRP. This is simply a nasty material, that keeps shedding fibers. Three successive coats of grey paint were applied in order to curb this behavior to some extent.
The GRP material absorbs the paint, almost like a piece of chalk. This means that the surfaces of this material are reasonably well sealed and the leakage of glass fibers is a thing of the past.
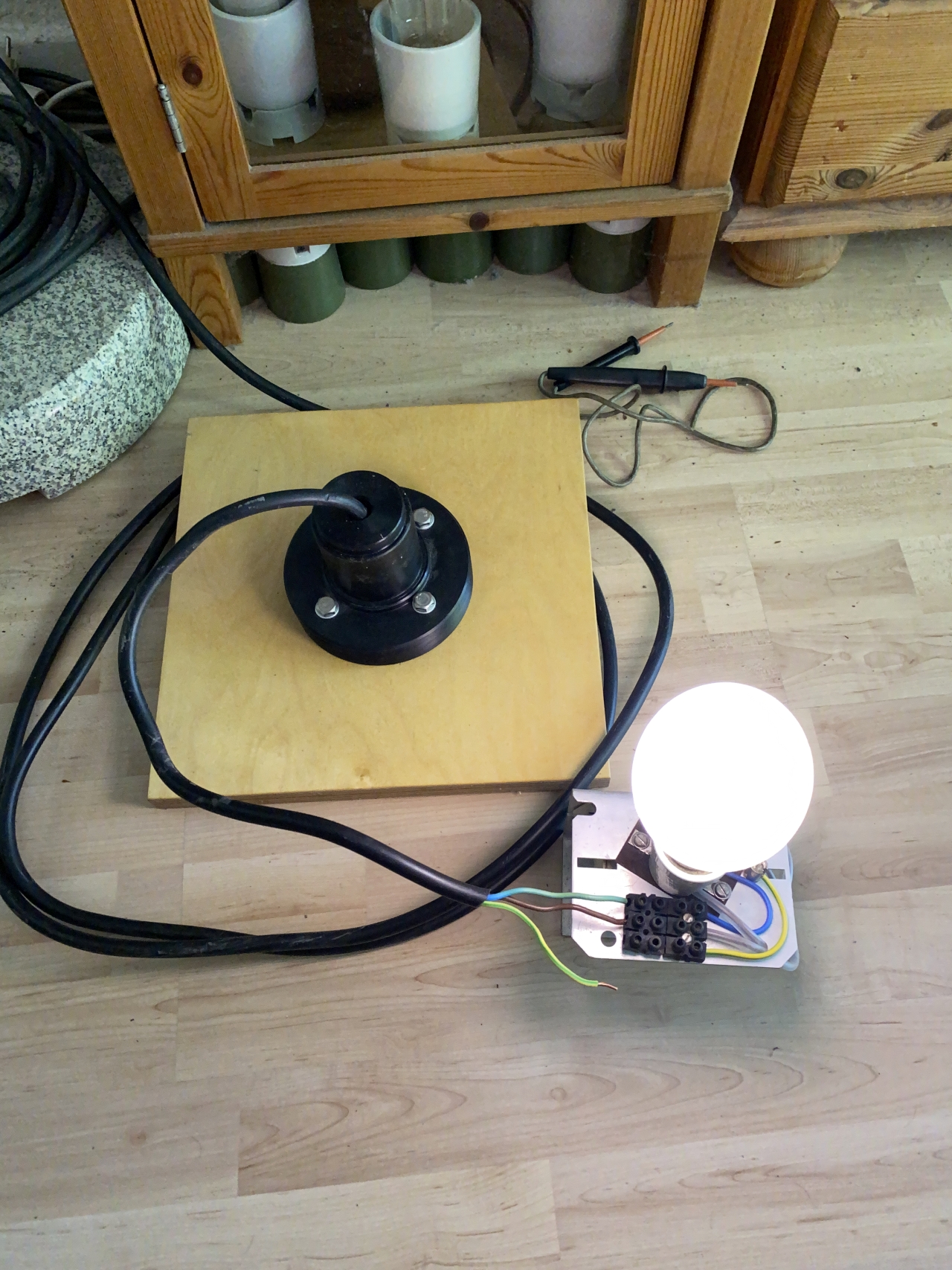
I made a turned part myself from black plastic material to hold the light. This was mounted on a wooden plate already prepared for this purpose. A channel for the connecting cable is milled into the wooden plate and 4 M8 drive-in nuts are fitted
in the holes on the underside of the wooden plate. The panel was made with drilling and milling by the joinery “around the corner”. The board also has 4 round felt elements in the corners on the underside. The sides and top were painted with wood oil.

I attached a round disk made of 4mm thick sheet aluminum to the upper part of the two threaded rods to protect the painted upper part from the direct radiant heat of the lamp.
So this is
not original, but a modification. It works very well and the top cover on the light only gets luke warm even after several hours of use.
I installed a used ballast from OPTIMA for 80W and 125W high-pressure mercury vapor lamps. I abandoned the original plan to fit a 125W lamp, because it was already unpleasantly bright for the living room.
A PHILIPS HPL-N 80W lamp has now been installed, which is perfectly adequate for this purpose.
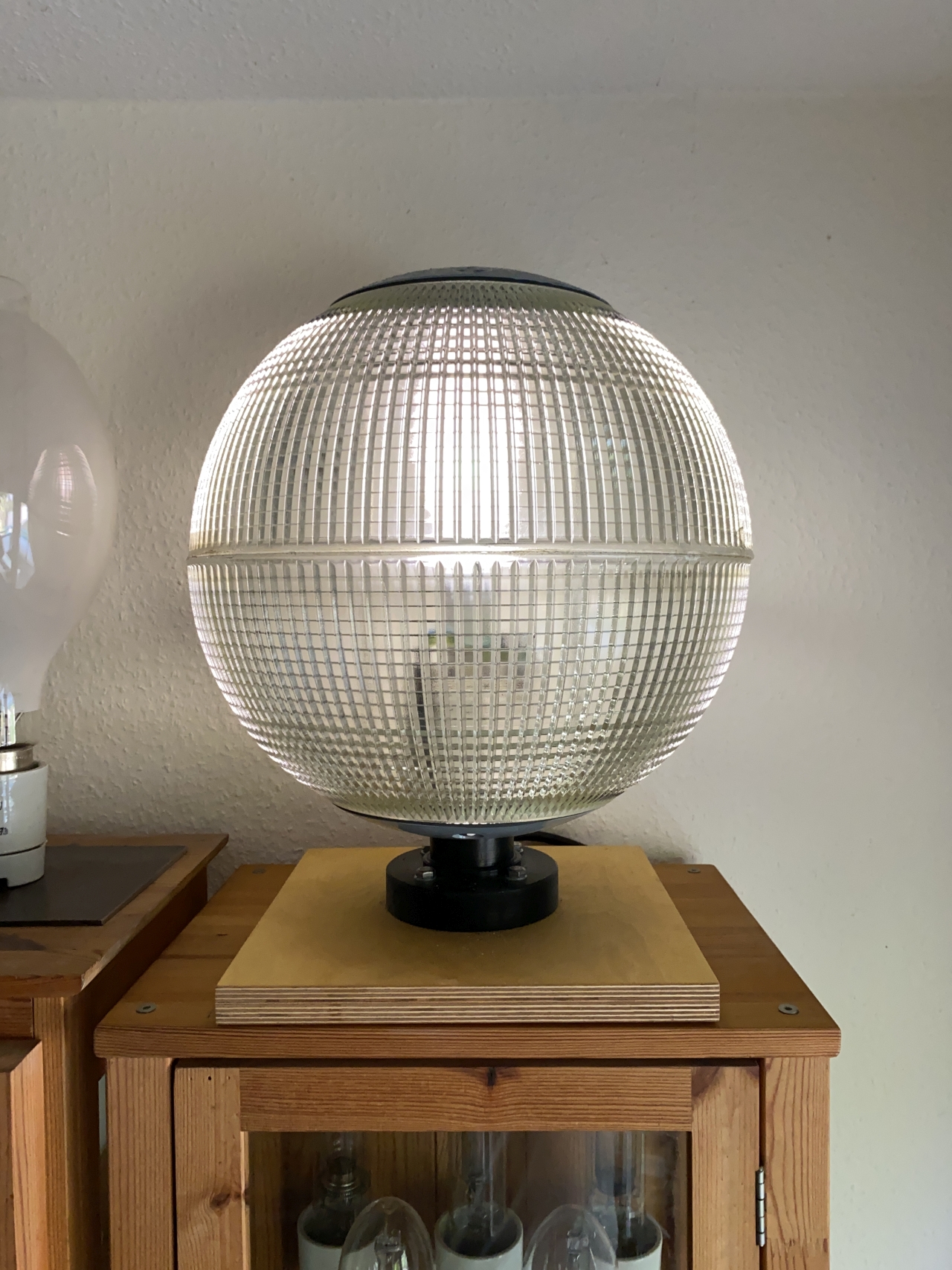
So you fiddle around with the part for weeks, painting, wiring, screwing, waiting for ordered spare parts (M8 cage nuts in this case) and “all of a sudden” the fixture is finished. As with many other projects,
you don't see all the time spent later on. In any case, I'm delighted with one of my new light sources in the living room.
Kind regards
Olav